Digital Twin in Manufacturing
The hype around “Digital Twin” has been building over the last few years! Does it work? Are we ready to use such a technology? Here is your quick guide to digital twins, what they are and why they matter for your organization.
First of all, we need to recognize that today, when we design machines, it is and must be for a connected world. If you are not, then you will lose out to competition sooner or later! As our assets and systems become more complicated, the way in which we develop for, manage and maintain them needs to evolve, too. We need tools to meet the new realities of software-driven products fuelled by digital disruption.
Digital twins give us a glimpse into what is happening, or what can happen, with physical assets now and far into the future.
Digital twins let us understand the present and predict the future
What this means is that a digital twin is a vital tool to help engineers and operators understand not only how products are performing, but how they will perform in the future. Analysis of the data from the connected sensors, combined with other sources of information, allows us to make these predictions.
With this information, organizations can learn more, faster. They can recreate boundaries surrounding product innovation, complex lifecycles, and value creation.
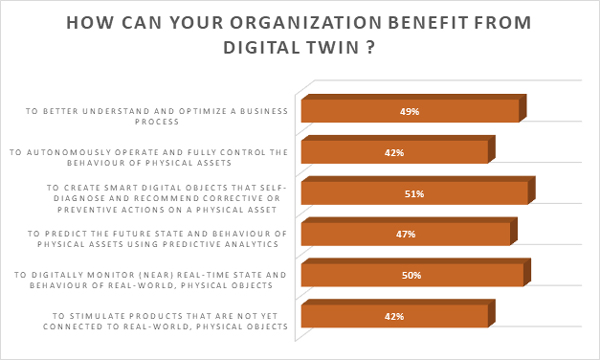
Benefits of Digital Twin for Engineers & Manufacturers
- Accelerated risk assessment and production time
- Optimize design & manufacturing process
- Real-time remote monitoring & Predictive maintenance
- Improved team collaboration & Operational Training
- Data-backed financial decision-making
Why do you need Digital Twin?
- Faster time to market – With such a comprehensive virtual representation, engineers can conduct a wide range of simulations to identify space constraints and potential bottlenecks so that they are resolved before installation.
- Operational Training – Safe learning with contextual information and digital modes using AR and VR technology, provides operators with professional competencies.
- Process optimization – Data and KPIs can offer precious insights to not only the top brass but also the folks who work on the shop floor, allowing them to streamline processes to always achieve optimal levels of production.
- Deriving actionable insights – data applications are built to track the performance of operational processes and articulate and solve the root causes of problems.
- Predicting future outcomes – data and analytics are used to automatically recognize patterns, by feeding large datasets into machine-learning algorithms to predict future behavior.
Creating real-world scenarios, virtually
An engineer testing a machine controls system, for example, would run a computer simulation to understand how the system would perform in various real-world scenarios. This method has the advantage of being a lot quicker and cheaper than building multiple physical cars to test. But there are still some shortcomings.
First, computer simulations like the one described above are limited to current real world events and environments. They can’t predict how the machine will react to future scenarios and changing circumstances. Second, modern machines are more than mechanics and electrics. They’re also comprised of lines of code.
This is where digital twin and the IoT come in. A digital twin uses data from connected sensors to tell the story of an asset all the way through its life-cycle. From testing to use in the real world. With IoT data, we can measure specific indicators of asset health and performance, like temperature and humidity, for example. By incorporating this data into the virtual model, or the digital twin, engineers have a full view into how the car is performing, through real-time feedback from the vehicle itself.
The value of a Digital Twin: Understanding Product Performance
Digital twins give businesses an unprecedented view into how their products perform. A digital twin can help identify potential faults, troubleshoot from afar, and ultimately improve customer satisfaction. It also helps with product differentiation, product quality, and add-on services, too.
If you can see how customers are using your product after they’ve bought it, you can gain a wealth of insights. That means you can use the data to (if warranted), safely eliminate unwanted products, functionality, or components, saving time and money.
There are other advantages to a digital twin, too. One of the major ones is that digital twins afford engineers and operators a detailed, intricate view of a physical asset that might be far away. With the twin, there’s no need for the engineer and the asset to be in the same room, or even the same country.
Digital twins address transformation industrial trends.
Hyper-automation, machine feedback from sensors; low-code cost reductions can help machine builders and their customers.
Overcoming obstacles to digital twins can accelerate time to market.
Consider this, how are you using digital twins to address industry demands and increase competitiveness?
About the Author
Senthil Kumar Deivasigamany is the Director of MN Engineering Solutions Inc. and an accomplished leader with a proven track record of building and growing businesses from scratch. He may be reached at senthil.kumar@mnengineeringsolutions.com.