Expand Your Employee Attraction, Preparation and Retention Efforts by Leveraging Industry 4.0 Technologies
Nearly every industry faces challenges around attracting, rapidly upskilling and retaining highly talented people. Each of these have their own nuances. Equally, there are many potential solutions, and Industry 4.0 offers plenty of tools and technologies that can help employers address these challenges.
When it comes to retention, the problems—and the solutions—often occur in the realms of communication, recognition and mutual respect. There are Industry 4.0 technologies that can, for instance, improve lines of communication between managers and production floor workers or between workers on different shifts. But much of the retention challenges related to Industry 4.0 come from the friction between people and technology. For a great overview of retention challenges and examples of what business leaders can do and are doing to respond, check out HR4.0: Shaping People Strategies in the Fourth Industrial Revolution published by the World Economic Forum.
For the rest of this article, let’s focus on attraction and preparation.
The 2011 documentary film Miss Representation explored the question of why women are under-represented in positions of power and influence in America. Marian Wright Edelman, founder and president of the Children’s Defense Fund, summed it up well when she said, “You can’t be what you can’t see.” That sentiment just as readily applies to careers and goes way beyond gender.
The “dream jobs” of all young people directly correlate to what they’re exposed to and the pop culture in which they grow up. In the past, if you asked a kid what he or she wanted to be when they grew up, you might get answers like professional athlete, astronaut, teacher, doctor and nurse.
There was even a blip in the 1990s when lots of kids wanted to be a marine biologist thanks to the film Free Willy. The flipside of that is that if young people didn’t see certain professions in their day-to-day lives, on TV, or in the movies, they couldn’t imagine being them.
Things haven’t changed all that much for today’s youth, except for their pop culture inputs. In 2021, Junior Achievement sponsored a survey of teenagers between the ages of 13 and 17. Thirty-seven percent of
participants cited “social media influencers” as the primary inspiration for future career inspiration and 60 percent of the teens said they’re more interested in starting their own business than working a traditional 9-to-5 job. And a 2019 Harris Poll of 8-to-12-year-olds for the LEGO Group found that “YouTuber” was the number one career choice for 29 percent of the 3,000 kids surveyed.
Crazy? Not if you dive deeper into what these young people are really saying. A 2020 Dream Jobs Report from the Organization for Economic Cooperation and Development revealed that half of the responding
teenagers “have a deep sense of uncertainty about which traditional professions will even exist when they grow up.”
MMA has partnered with Automation Alley to present Navigating the Future: Global Industry 4.0 Trends, Standards & Policy. With insights from roundtable participants — leaders in industry, academia and government — the Integr8 Playbooks offer a monthly roundup of important digital transformation discissions and provides you with a wealth of insights and actionable strategies.
Access the full playbooks.
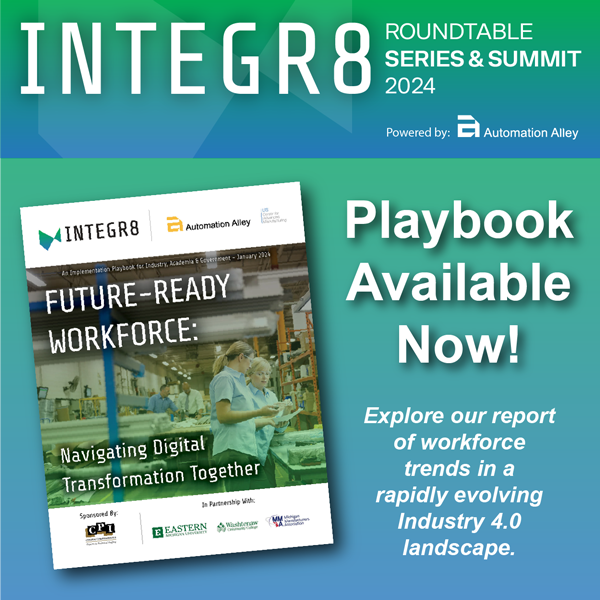
This persistent dread is fueled both by the amount of change these teens have lived through and by the messages they absorb from social and other media. And this translates into them being attracted to careers where they perceive they will have some measure of personal control and job security, where they will find purpose and fulfillment and where they’ll be able to “make a difference” in the world. So, it’s not YouTube or TikTok that’s the attraction, per se. It’s the sense of independence, impact and purpose.
Another interesting finding from nearly all these surveys and studies: many of these young people are most highly interested in careers that involve use of “lots of technology.” They see technology, digital devices and machines as conduits for creativity. According to the Nominex 2022 Digital Youth Index, many young people are attracted to opportunities “to develop skills that allow them to create hardware and/or software.” The age group most excited about such opportunities are 8- to 11-year-olds, but that enthusiasm continues at least through age 25 (which is generally the cap age for definition of “young adult”).
This presents a huge opportunity for manufacturers to capture the imaginations and interest of young people currently entering the job market and the next generation of talent. Manufacturers can benefit by association with cutting-edge technologies like additive, nano and bio/medical manufacturing, even if they aren’t directly or heavily involved in those sectors. The key top-line message is that manufacturing in its entirety is a high-tech industry with tons of opportunities for creative people who want to make a positive impact in the world.
On both the attraction and preparation fronts, manufacturers need to embrace and leverage technologies like augmented reality, robots and cobots and blended-learning approaches that use virtual simulators and labs in coordination with high-tech industry-equivalent manufacturing training equipment.
Tooling-U SME, for instance, has developed Virtual Lab packages that integrate immersive VR tech and curriculum with eLearning classes and Skills Guides. For more info, visit learn.toolingu.com and click the Virtual Labs link from the Manufacturing Products & Services menu.
Augmented Reality systems like those made by Michigan-based LightGuide, Inc. can be used both in the classroom and on the shop floor.
And a host of great standalone virtual and/or hardware simulators are available. Looking just at the area of CNC machining and cutting, for example, options range from the Haas Next Generation Control Simulator—a real full-function Haas hardware control panel and keypad with visual simulator—to full “digital twins” of entire CNC mills, lathes, waterjets, laser cutters and more that simulate Haas, Mazak, Hurco, Cincinnati, Siemens, Fanuc, Index, Doosan, Makino and other machine tools. The Michigan Manufacturing Technology Center staff is an excellent resource for exploring what’s available for training and/or in production environments.
Using these Industry 4.0 technology tools aren’t a good idea just because they’re attractive to young people. They’re also proven to lower the cost of training and speed up time-to-competency.
To really seal the deal on attracting and preparing new talent in Industry 4.0-related careers, consider supporting one or more industry-recognized certification efforts and training programs that integrate them. These include:
- Multiple Certified Industry 4.0 Associate, Specialist and Professional certifications from the Smart Automation Certification Alliance.
- Certified Additive Manufacturing Fundamentals and Technician certifications, Robotics in Manufacturing Fundamentals certification, Certified Manufacturing Technologist and Certified Manufacturing Engineer certifications from SME.
- Industry 4.0 Smart Production Specialist and Additive Manufacturing Designer certifications from NIMS.
- Certifications endorsed or offered by training curricula and systems developers like Amatrol, Festo and SMC.
Industry 4.0 may have started as an industrial revolution, but it’s also transforming delivery of skills training. In addition to changing the way manufacturers do business, Industry 4.0 can change the way you attract, prepare and retain highly skilled talent.
Learn More
John J. Walsh
MMA President & CEO
Call 517-487-8550
E-mail walsh@mimfg.org
Bill Rayl
Executive Director of Workforce Solutions
Call 517-487-8513
E-mail rayl@mimfg.org