The End of JIT: Adapting to the Global Supply Chain Shortage in 2022
The disruption of the global supply chain has rocked the U.S. manufacturing industry over the past two years. Millions of consumers felt the effect as products were delayed, never showed up and in some instances, were delivered with downgraded features.
But in 2022, after much of the country reopened and began operating as normal, manufacturers still faced a massive problem. There was still a shortage of supplies and components, which continued to make it difficult to keep up with pent-up consumer demand.
With no end in sight, manufacturers now need to adapt to shortages in the supply chain and future-proof their operations so they can overcome further interruptions. But there’s one key obstacle they still need to overcome — the limitations of Just-in-time Manufacturing.
The End of Just-in-time Manufacturing
The pursuit of greater efficiency has always been the goal for manufacturers. When Japan introduced the lean, or Just-in-time (JIT), philosophy in the 1970s, it revolutionized the industry.
JIT manufacturing focuses on speeding up production and lowering costs by limiting inventory on-hand and replenishing it whenever it is needed. If you aren’t familiar with it, the most common analogy is one of a ship sailing over rocks. Water is the inventory, and the rocks represent your processes and systems. When the water is too high, you’re sailing easily but likely wasting money by holding excess inventory. When the water is too low, your ship crashes into the rocks.
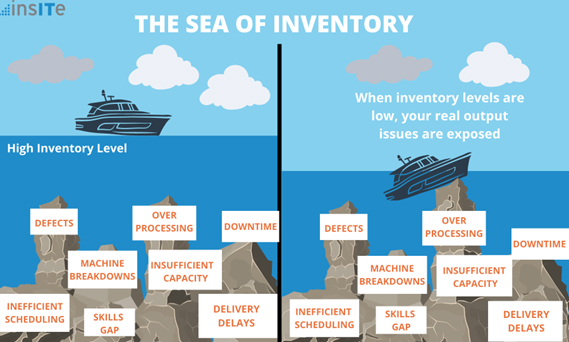
Although it only rose to popularity decades later, JIT became the global standard and companies saw significant growth after implementing it, which included an exponential reduction in lead times, labor costs and space.
The current supply chain crisis broke JIT manufacturing.
What the JIT methodology failed to consider was widescale disruption. Companies looked for the most affordable way to get quality parts, which often meant looking at international suppliers instead of local ones.
Now that suppliers overseas are unable to give them crucial components, they are scrambling to react and struggling to meet consumer demand.
The 5 Main Supply Chain Issues for US Manufacturers
When we study the different challenges that organizations are dealing with in 2022, we can boil most of them down to five key issues:
- An overreliance on international suppliers
- A failure to reprioritize product lines quickly enough
- Transportation issues including insufficient ships and rising costs
- A nationwide shortage of skilled labor
- Technology that fails to adapt to an agile process
It could take years before the entire supply chain resets itself. Especially as warehouses in China continue to jam up due to COVID-19 restrictions, there are delivery delays through Europe because Russia invades Ukraine and major ports are over capacity.
The current supply chain process needs a refresh.
How to Adapt to the Supply Chain Shortage
How can manufacturers adapt to shortages in the supply chain? They need to prioritize their systems based on margins and not just avoid bottlenecks, turn to a more diverse group of local suppliers and increase inventory levels.
But for this to happen, organizations should turn to Industry 4.0 technology, which would allow them to respond to changes in the supply chain faster and minimize its effects. Manufacturers need real-time information available to everyone in the organization, the ability to collaborate more effectively and the need to discover opportunities to become “lean.”
Here are the four steps manufacturers need to take to adapt to the supply chain shortage:
- Connect
- Collect
- Analyze
- Automate
Connect the Top Floor to the Shop Floor
Management cannot always spend time on the production floor, which makes it difficult to address workflow inefficiencies when they arise.
Embracing digital transformation is the logical solution. Digital transformation is about augmenting your current workforce with Industry 4.0 technologies.
If it produces data, it should be connected and measured. And not just in a spreadsheet that is e-mailed around the organization. True connection, especially in hybrid work environments, means that the data needs to be accessible from any location and any device.
Collect Data from Across Your Entire Operation
With a connected shop floor, you can take data from various sources and make sense of it. This provides you with actionable insights so you can prioritize your production.
As inventory gets tighter, you can decide which items to schedule next to meet your deadlines. This is true when it comes to collecting external data as well, including transportation costs, supplier capacity and component delivery.
Analyze Trends, Anomalies and Patterns
If it matters to your customers, it should be visible and clear. Having access to better data is crucial. But, while data is important, you need to be able to make sense of it all.
When you can visualize production data end-to-end, you can increase that visibility across the entire organization making it easier to determine trends, anomalies and patterns in your operations.
Automate Your Time-consuming Tasks
From data entry to defect detection — if it is repeatable, it should be automated.
By leveraging artificial intelligence, you can streamline many time-consuming, laborious tasks and position your business to scale despite disruptions to your supply network. It also frees your internal teams to focus on the most key areas of your business and adapt to changes in production.
Looking Ahead to the Future of the Supply Chain
The manufacturing industry’s current supply chain challenges are not going away anytime soon. There will be more parts, components and chips that fail to get delivered on time.
US manufacturers should lead the way in pivoting from a JIT manufacturing model to a more diverse, connected and resilient supply chain. One that allows them more control over their production and their growth.
About the Author
Dave Poggi brings more than 30 years of experience in manufacturing, distribution, and supply chain IT. As the CEO and a principal consultant at Software InsITe, he is highly skilled in developing and executing integrated strategies that maximize business results through technology. He has expertise in leading ERP, shop floor, applications development, collaboration, and analytics projects. He may be reached at 616-485-2700 or dave.poggi@softwareinsite.com.
InsITe is an MMA Premium Associate Member and has been an MMA member company since September 2020. Visit online: trustedinsite.com.